
86 17344894490
service@chalcoaluminum.com
- Ánodo de sacrificio de aleación de aluminio
- Ánodo de sacrificio de aleación de magnesio
- Serie de protección catódica de corriente impresa
Perfiles extruidos de aleación de aluminio para carril
A principios de la década de 1950, los países desarrollados como Europa, América y Japón comenzaron a utilizar perfiles de aluminio para fabricar vehículos ferroviarios. En la actualidad, los materiales de aleación de aluminio se han utilizado ampliamente en las carrocerías nacionales de trenes de alta velocidad. El desarrollo de la carrocería de perfil de aluminio en China comenzó en la década de 1990. En la actualidad, tres de los cuatro tipos de EMA utilizados en la línea dedicada al pasajero del ferrocarril están hechos de aleación de aluminio. Esto refleja las ventajas del perfil de aluminio en la aplicación de la carrocería de los vagones de tránsito ferroviario. Realice un peso ligero, ahorro de energía y reducción de consumo. Los perfiles extruidos de aleación de aluminio para riel son el mejor material para la carrocería ligera de un automóvil. Debido a su baja densidad, excelente resistencia específica y excelente tenacidad plástica, el perfil de aluminio no solo puede cumplir con los requisitos de seguridad del ferrocarril de alta velocidad, sino también reducir en gran medida el peso muerto del tren. En términos generales, la aleación de aluminio utilizada en un vagón de ferrocarril de alta velocidad es de aproximadamente 9 toneladas, que es un 30% - 50% menos que la de todo el acero. Además, por cada reducción del 10% en el peso, el combustible se puede ahorrar en un 8%, y el efecto del ahorro de energía y la reducción del consumo es obvio.
Perfiles extruidos de aleación de aluminio para carril
Los perfiles extruidos de aleación de aluminio para riel son fáciles de procesar y formar, y el ciclo de fabricación es corto. La aleación de aluminio tiene un excelente rendimiento de procesamiento y moldeo y rendimiento de soldadura del módulo. Puede producir perfiles de sección grande, de forma especial, de paredes delgadas y huecos de hasta más de 30 metros en una sola extrusión, y tiene un buen rendimiento. En el proceso de fabricación de carrocerías de automóviles, los perfiles de aluminio solo necesitan blanking, ensamblaje y ensamblaje y soldadura de robots grandes. En comparación con la producción de carrocería de automóvil de chapa de acero, tiene las ventajas de un proceso simple, ahorro de tiempo y material, bajo costo y ciclo corto.
Los perfiles extruidos de aleación de aluminio para riel tienen una excelente resistencia a la corrosión y una larga vida útil. Una película de óxido denso es fácil de formar en la superficie de la aleación de aluminio, que tiene una excelente resistencia a la corrosión en el entorno atmosférico. Si se adopta el anodizado, la electroforesis, la pulverización y otros tratamientos superficiales, la resistencia a la corrosión del perfil de aluminio se puede mejorar aún más, lo que es propicio para prolongar la vida útil de la carrocería del automóvil. Mantenimiento sencillo y fácil reciclaje. La carrocería del automóvil de aleación de aluminio es fácil de reemplazar sin eliminación de óxido. Es adecuado para diversos tratamientos superficiales y fácil de mantener. El costo de mantenimiento es solo el 52% del de la carrocería de acero. Es fácil reciclar y ahorrar recursos. El valor de reciclaje es aproximadamente 4,8 veces mayor que el del acero.
Los perfiles extruidos de aleación de aluminio para carril son en su mayoría perfiles anchos, de forma especial, de paredes delgadas y huecos, que son propensos a la distorsión, deformación y otros defectos durante el tratamiento térmico. En la actualidad, la mayoría de las empresas utilizan equipos de enfriamiento refrigerados por aire en línea. Para los perfiles de carrocería de automóviles, la intensidad de enfriamiento es baja y la uniformidad de enfriamiento no es suficiente, lo que resulta en un rendimiento bajo o desigual de los perfiles; Para algunos perfiles de carrocería de automóviles con gran diferencia de espesor de pared, la intensidad de enfriamiento en la pared gruesa es menor, lo que resulta en granos gruesos en el centro y una mayor heterogeneidad estructural. Con el objetivo de la alta eficiencia y uniformidad del enfriamiento y la complejidad de la sección del perfil, se desarrolla un equipo de enfriamiento automático que integra enfriamiento por aire, enfriamiento por niebla de aire y enfriamiento por agua, que puede controlar de forma independiente la intensidad de enfriamiento de cada parte, lo que desempeña un gran papel en la mejora del rendimiento del perfil.
Para algunos componentes específicos de la carrocería del vehículo, como la luz transversal y la viga de tracción, es necesario cumplir con un alto rendimiento de fatiga y corrosión bajo tensión. Para mejorar el rendimiento de fatiga, no solo se debe adoptar el proceso avanzado de fusión y fundición para garantizar que no haya defectos metalúrgicos en el material, sino que también se debe reducir la fase cristalina quebradiza gruesa a través de un tratamiento de homogeneización de múltiples etapas para reducir la sensibilidad a la grieta del material; Para el rendimiento de corrosión bajo tensión, también es necesario desarrollar nuevos procesos de envejecimiento, como el envejecimiento gradual y el envejecimiento no isotérmico, a fin de mejorar las características del límite de grano con la premisa de garantizar una excelente plasticidad fuerte, hacer que la segunda fase del límite de grano se distribuya intermitentemente y la zona libre de precipitación (PFZ) sea más estrecha.
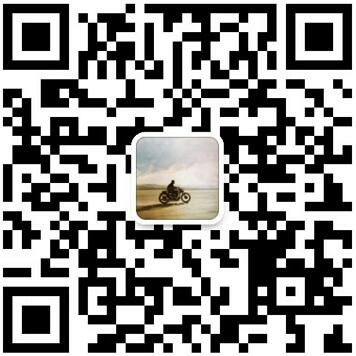
Oferta gratuita de productos, bienvenido a consultar en cualquier momento, daremos la primera respuesta. Nuestro correo electrónico: