
86 17344894490
service@chalcoaluminum.com
- Ánodo de sacrificio de aleación de aluminio
- Ánodo de sacrificio de aleación de magnesio
- Serie de protección catódica de corriente impresa
Piezas estructurales de perfil de aluminio extruido en la fabricación de vehículos
Según la información, alrededor del 60% de los pedidos existentes de los fabricantes europeos de locomotoras y vehículos son vehículos con carrocería de aluminio. Hace 20 años, tales pedidos eran solo del 2% al 3%. Ahora la estructura de aluminio se ha aplicado en hielo, tgv-2n, etr460, etr500, tren talgo hotel y otros trenes de alta velocidad, así como en muchos vehículos de transporte ferroviario suburbano y urbano.
La adopción de piezas estructurales de perfil de aluminio extruido comenzó a principios de la década de 1970. En ese momento, el progreso científico y tecnológico en la aplicación de perfiles de aluminio había hecho posible hacer componentes de aluminio de acuerdo con la forma y el tamaño requeridos. Este componente de aluminio se ha aplicado a la carrocería inclinable de los trenes aptos en Gran Bretaña. Sin embargo, en ese momento, la aplicación de componentes de aluminio extruido no produjo grandes beneficios, es decir, los precios más altos de los materiales no se compensaron por la reducción de la carga de trabajo de fabricación. En ese momento, el uso de piezas estructurales de gran tamaño solo redujo la carga de trabajo de producción de la carrocería del automóvil en un 40%, y redujo el peso muerto de la carrocería del automóvil de 26 m de largo a 7,5 t, mientras que el peso muerto de la carrocería de acero de 26 m de largo era de 11 T. En la década de 1970, el departamento ferroviario prestó más atención al cálculo del costo total de toda la vida útil de los vehículos (costo de compra más costo de operación y mantenimiento). Se dieron cuenta de que el consumo de energía de tracción del tren debe mantenerse al mismo nivel, lo que depende en gran medida del peso propio del material rodante.
Más tarde, algunas nuevas medidas técnicas y tecnológicas, la más importante de las cuales se logró a mediados de la década de 1980, como la adopción del método de extrusión de piezas estructurales de gran tamaño de carcasa de doble capa, que redujo la necesidad de fijaciones transversales al mínimo, redujeron aún más el tiempo de producción de la carrocería de aluminio del vehículo, reducido en un 50% en comparación con los vehículos de acero, y ha sido posible hacer un cuerpo de cilindro de doble capa de acuerdo con el método convencional, y luego la apertura de agujeros de ventana Las operaciones de soldadura se completan en el proceso de operaciones técnicas unificadas, solo parcialmente utilizando tecnología y equipos de robots.
Ahora, cuando los departamentos ferroviarios reducen gradual y más su participación en el desarrollo de nuevos vehículos e implementan políticas de compra para reducir los costos iniciales de fabricación y los gastos operativos futuros, los fabricantes tienen mayor libertad para adoptar nuevas estructuras y materiales para satisfacer los requisitos técnicos de los suscriptores y adaptarse a la tendencia de desarrollo del mercado. Las piezas estructurales de perfil de aluminio extruido también tienen otras ventajas al cumplir con algunos requisitos estrictos para la estructura del vehículo. Por ejemplo, la rigidez de la estructura de extrusión de carcasa de doble capa puede garantizar que el impacto aerodinámico producido cuando el tren de alta velocidad se encuentra tenga una resistencia especial al impacto. Otra característica importante de la carrocería del automóvil con esta estructura es su gran rigidez longitudinal. La relación de rigidez longitudinal y transversal puede alcanzar 70:30, mientras que la relación de la carrocería de acero del automóvil es de 40:60. Además, los perfiles de aluminio también pueden cumplir con los requisitos de buena forma externa, sin el uso de rellenos y mucho trabajo manual. Por ejemplo, para algunos modelos del Ferrocarril Federal Alemán, dado que no se utiliza ningún relleno, después del cálculo, junto con el recubrimiento de pintura, el peso propio puede ser de 500 kg.
El uso de piezas estructurales de perfil de aluminio extruido también hace que los fabricantes de vehículos se enfrenten a tareas complejas. Deben encontrar un equilibrio entre la mano de obra y los precios de los materiales, y hacer que los diseñadores se esfuercen por lograr este equilibrio. Debe aclararse que el material es solo un factor en todo el concepto. El proceso de producción y el proceso técnico adoptado también deben formularse en detalle para que se ajuste a la capacidad de producción de la empresa y se equilibre con la inversión.
Por ejemplo, para la mayoría de las empresas de fabricación de máquinas, minimizar las reservas de medios de producción es una prioridad. La elección de materiales y procesos por parte de los diseñadores tiene un impacto significativo en esto. ABB tiene una línea de producción que puede producir 8 vehículos con carrocería de aluminio cada semana, lo que reduce el costo total de almacenamiento de material en un 8%. Sin embargo, este equilibrio se destruye fácilmente debido a los cambios en el proceso técnico causados por el uso de materiales. Por ejemplo, cuando la transición de la soldadura a la unión requiere más reservas diarias para compensar el tiempo considerable requerido para el endurecimiento de la unión.
Otro proveedor líder de perfiles de aluminio para la fabricación de material rodante es la empresa alemana de VCM. Los líderes de la compañía prevén que existe una gran tendencia de desarrollo en la estandarización de la estructura del vehículo y la adopción del método de diseño de módulos (esta tendencia se ha fortalecido debido a la demanda del mercado, por lo que cuenta con el apoyo de los fabricantes), y creen que teniendo en cuenta la demanda del mercado para la regionalización del transporte ferroviario local en Alemania, algunas empresas privadas prestarán más atención al uso de la estructura de módulos estandarizados para satisfacer en mayor medida los requisitos de los ordenantes individuales. En la actualidad, varios fabricantes europeos de locomotoras y vehículos tienen un gran número de ideas de diseño, y estas ideas se basan en el diseño de módulos. Esta transformación hacia la estandarización y la modularidad es beneficiosa tanto para los productores como para los usuarios. La expansión del uso de perfiles de aluminio en la fabricación de vehículos reducirá en gran medida el ciclo de producción debido al uso más amplio de la soldadura automática.
También es obvio que los vehículos de carrocería de aluminio soldado tienen una alta resistencia a la carga de impacto, lo que es propicio para mejorar la seguridad de conducción. ABB invirtió 1 millón de libras para organizar y llevar a cabo la prueba de destrucción de la estructura de aluminio, y obtuvo resultados satisfactorios y, lo que es más importante, los resultados esperados de la prueba. La compañía también ha acumulado una valiosa experiencia práctica en la reparación de los métodos de falla de los vehículos accidentados. A principios de 1994, la prueba de daños en la muestra de prueba de automóvil de pasajeros de dos pisos del tren tgv-2n ordenada por GEC Alstom en Francia demostró que cuando la fuerza de impacto era de 250 t, debido a la energía de impacto absorbida de 8 mj, la estructura se extruyó por un total de 80 cm y el cuerpo de aluminio permaneció intacto en su conjunto.
Al mismo tiempo, el reconocimiento de las ventajas de la carrocería de aluminio no está exento de problemas. Los fabricantes de locomotoras y vehículos de carrocería de acero expresaron su preocupación por el énfasis en el aluminio en el proceso de fabricación de trenes de hielo en Alemania, y llevaron a cabo un estudio para confirmar la superioridad del acero en 1994. Sin embargo, como antes, el uso de estructura de acero conduce a un aumento de alrededor del 20% en el peso muerto de la carrocería del automóvil.
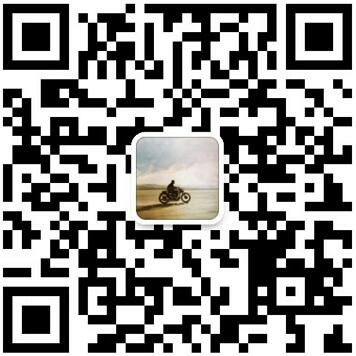
Oferta gratuita de productos, bienvenido a consultar en cualquier momento, daremos la primera respuesta. Nuestro correo electrónico: